Who Else Wants Info About How To Create A BOM In SAP
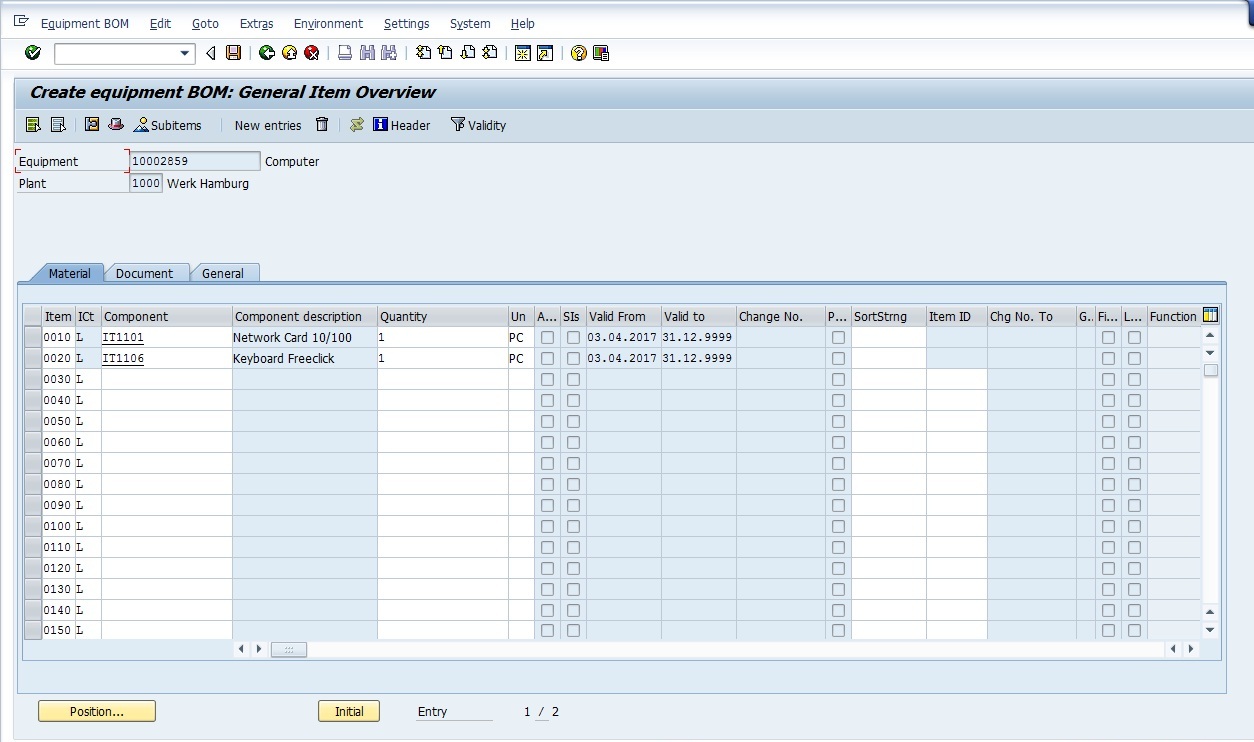
SAP PM Bills Of Material Free Online Training Tutorial
Bill of Materials (BOM) in SAP
Ever wondered how SAP knows exactly what ingredients you need to bake that perfect product? The secret ingredient isn't love (though that helps!), it's the Bill of Materials, or BOM. Think of it as a meticulously detailed recipe, listing every component, assembly, and raw material required to create something tangible. So, lets dive in and discover how to create a BOM in SAP!
1. What Exactly is a BOM and Why Should I Care?
Imagine trying to build a Lego castle without instructions. Chaos, right? A BOM prevents that chaos in manufacturing. It's a structured list that tells SAP (and everyone involved) precisely what's needed, in what quantity, and in what order to assemble a product. Without a BOM, you risk shortages, delays, and potentially a whole lot of wasted resources.
A well-maintained BOM is more than just a list; it's the backbone of your production planning. It drives material requirements planning (MRP), costing, and even procurement. It ensures you have the right stuff, at the right time, at the right price. Plus, it allows for accurate costing — knowing exactly what it costs to make something is pretty vital, wouldnt you agree?
Consider this: Your company manufactures bicycles. The BOM for a bicycle would include things like the frame, wheels, tires, handlebars, seat, gears, brakes, and all the nuts and bolts to hold it together. Each item has a specific quantity, and potentially even a sequence for assembly. Keeping this information organized and accessible is what a BOM is all about.
Finally, a robust BOM is essential for regulatory compliance. In certain industries, you must be able to trace all the components in your product back to their origins. A good BOM system facilitates this traceability, helping you avoid potential fines and legal headaches.
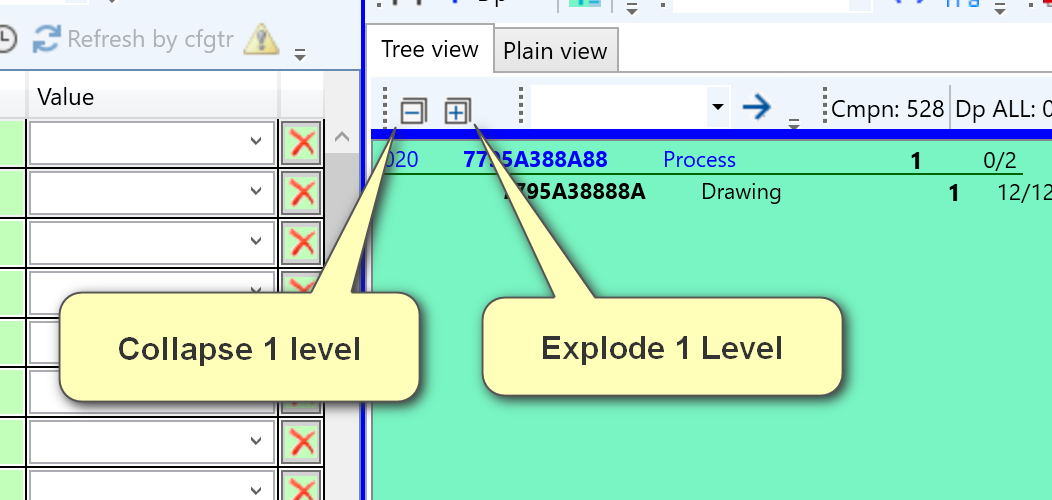
6 BOM Analyzer MultiLevel Visual For SAP
Step-by-Step
Alright, let's get down to the nitty-gritty (oops, almost slipped up!). Creating a BOM in SAP might seem daunting at first, but it's a fairly straightforward process once you get the hang of it. Think of it as following a slightly complicated recipe — just stick to the steps!
2. Accessing the BOM Transaction
First, you need to access the relevant transaction in SAP. The primary transaction code for creating and maintaining BOMs is CS01 (Create Material BOM), CS02 (Change Material BOM), and CS03 (Display Material BOM). You can enter these codes directly into the SAP command field, or navigate through the SAP menu structure to find the appropriate option.
Using the transaction code is the fastest and most efficient way. So, type 'CS01' into the command field and hit enter. This will open the initial screen for creating a new material BOM. Easy peasy!
The initial screen will prompt you for some essential information, such as the material number, plant, and BOM usage. The material number is the unique identifier for the finished product that the BOM represents. The plant specifies the location where the BOM will be used. The BOM usage defines the purpose of the BOM (e.g., production, engineering). Make sure you select the correct usage to avoid issues later on.
Choosing the correct plant is also crucial. A BOM created for one plant might not be valid for another due to differences in manufacturing processes or available components. So, double-check that you've selected the right plant before proceeding. After entering the required information, press Enter to move to the BOM maintenance screen.
3. Adding Components to the BOM
This is where the real fun begins! On the BOM maintenance screen, you'll start adding the individual components that make up your product. For each component, you'll need to specify the material number, quantity, and unit of measure.
You can manually enter each component, or, if you have a large BOM, you can use the copy functionality to import components from an existing BOM. This can save you a considerable amount of time and effort.
Pay close attention to the quantities you enter for each component. An incorrect quantity can lead to shortages or overstocking. Double-check your numbers to ensure accuracy. Also, make sure the unit of measure is correct. For example, you might need 10 meters of wire, not 10 pieces.
SAP allows you to specify different item categories for BOM components. Common item categories include stock items (materials that are managed in inventory), non-stock items (materials that are not managed in inventory), and variable-size items (materials that are measured by length or area). Selecting the correct item category is important for proper inventory management and costing.
4. Maintaining Item Details
Each component in your BOM has several details associated with it. You can maintain these details by selecting the component and clicking on the "Item" button. This will open a screen where you can specify information such as the component's description, lead time offset, and scrap percentage.
The lead time offset allows you to specify a delay in the start time for a particular component. For example, if a component requires a special treatment that takes a few days, you can use the lead time offset to account for this delay in your production schedule.
The scrap percentage allows you to account for material that is lost or damaged during production. For example, if you typically lose 5% of a certain component due to breakage, you can enter a scrap percentage of 5%. This will ensure that SAP orders enough of the component to account for the anticipated scrap.
You can also add notes and attachments to each component. This can be useful for providing additional information or instructions to the production team. For example, you might attach a drawing of the component or a document outlining specific quality requirements.

SAP PP BOM Active Version & Inactive Check... Community
Advanced BOM Features
SAP offers a range of advanced BOM features that can help you streamline your production process and improve accuracy. These features can be particularly useful for complex products with many components.
5. Variant BOMs
If you manufacture products with multiple variations, you can use variant BOMs to manage the different configurations. A variant BOM allows you to define a base BOM and then specify the components that are different for each variation.
For example, if you manufacture bicycles in different colors, you could create a base BOM that includes all the common components (frame, wheels, tires, etc.) and then create variant BOMs for each color, specifying the color of the frame and any other color-specific components.
Variant BOMs can save you a significant amount of time and effort compared to creating separate BOMs for each variation. They also make it easier to manage changes to the base BOM, as the changes are automatically applied to all variant BOMs.
Setting up variant BOMs requires a bit of initial configuration, but the long-term benefits are well worth the effort. Consult your SAP documentation or a qualified consultant for assistance with setting up variant BOMs.
6. Phantom Assemblies
A phantom assembly is a temporary assembly that is used only for production planning purposes. It's not actually stocked in inventory. Phantom assemblies can be useful for simplifying complex BOMs and for managing the flow of materials through the production process.
For example, you might create a phantom assembly for a sub-assembly that is manufactured in a separate department and then immediately consumed in the final assembly. The phantom assembly would not be stocked in inventory, but it would be used to plan the production of the sub-assembly and to ensure that it is available when needed.
Phantom assemblies can help you reduce the number of materials that need to be managed in inventory and can simplify the planning process. However, it's important to use them judiciously, as they can also make the BOM more complex if not used correctly.
Think of phantom assemblies as a way to "hide" some of the complexity in your BOM. They're like the backstage crew in a theater production — you don't see them, but they're essential for making the show run smoothly.

Troubleshooting Common BOM Issues
Even with the best planning, things can sometimes go wrong. Here are some common BOM issues and how to troubleshoot them.
7. Missing Components
One of the most common BOM issues is missing components. This can happen if a component is not included in the BOM, or if the quantity of a component is incorrect. If you encounter a shortage of a particular component, the first thing you should do is check the BOM to ensure that the component is included and that the quantity is correct.
If the BOM is correct, the issue may be related to inventory management or procurement. Check your inventory levels to ensure that you have enough of the component on hand. If you don't, check with your procurement department to see if there are any delays in the delivery of the component.
Sometimes, a missing component can be due to a change in the design of the product that was not properly reflected in the BOM. Make sure that your engineering and production teams are communicating effectively to ensure that the BOM is always up-to-date.
Missing components can cause significant delays in your production process. By proactively monitoring your BOM and inventory levels, you can often prevent these issues from occurring in the first place.
8. Incorrect Quantities
Another common BOM issue is incorrect quantities. This can happen if the quantity of a component is entered incorrectly, or if the unit of measure is incorrect. If you notice that you are consistently running out of a particular component, or that you have a large surplus of a component, check the BOM to ensure that the quantity is correct.
Pay close attention to the unit of measure. For example, you might need 10 meters of wire, not 10 pieces. Using the wrong unit of measure can lead to significant errors in your production planning.
Also, consider the scrap percentage for each component. If you typically lose a certain percentage of a component due to breakage, make sure that you account for this in the BOM. Otherwise, you may consistently underestimate the quantity of the component that you need.
Regularly review your BOMs and compare them to your actual production data to identify any discrepancies. This will help you catch any errors early on and prevent them from causing significant problems.

FAQ
Still have questions? No problem! Here are some frequently asked questions about BOMs in SAP.
9. Q
A: A single-level BOM lists only the components directly used to make a finished product. A multi-level BOM shows the entire hierarchy of components, including sub-assemblies and their components. Think of it as a family tree — a single-level BOM shows only the children, while a multi-level BOM shows the grandparents, parents, and children!
10. Q
A: Absolutely! BOMs can be used for various purposes, including production planning, costing, and engineering. In fact, different "BOM usages" can be defined in SAP to specify the intended purpose of a particular BOM. So yes, your engineering team and your production team can both leverage the power of a well-maintained BOM.
11. Q
A: As often as necessary! Any time there's a change to the product design, materials used, or manufacturing process, you should update your BOM. Regular reviews are also a good idea to ensure accuracy and prevent errors. Treating your BOMs like living documents is the key to keeping your production running smoothly.
